LEAN SIX SIGMA FOUNDATIONS WORKSHOP
Transform Your Business with Proven Strategies for Efficiency and Quality Improvement
- Evolution of Lean Management
- The 'Toyota Production System'
- Process Simulation and Analysis
- What is Lean Six Sigma?
- Lean Six Sigma Example
- How to Implement Lean Six Sigma
- The 'Lean Six Sigma Transformation'
- Presentation of Results from an Actual Lean Six Sigma Implementation
- Lean Six Sigma Exercise (through process videos)
- A Case Study (if time available)
- Lean Six Sigma Yellow Belt Certification Exam Registration for Participants
- Post Workshop Activity Guideline
- Instructor
The workshop covers the following
⬇
Evolution of Lean Management
Lean Six Sigma management has evolved from traditional craft production, where highly skilled workers used simple tools to build customized items at high costs, to mass production, which emphasized standardized parts, high volume, and lower costs at the expense of variety. A notable example is the Ford Model T assembly line, where task cycles were dramatically reduced from 514 minutes to just 1.19 minutes through innovations such as the moving assembly line.
The ‘Toyota Production System’
The Toyota Production System (TPS) is a cornerstone of Lean Six Sigma. It emerged as an innovative approach to manufacturing that combined the advantages of craft and mass production. Inspired by a visit to Ford’s plant in 1950, Eiji Toyoda and Taiichi Ohno developed a system to address the unique challenges of the Japanese market. TPS focuses on reducing waste (muda) and improving efficiency through practices such as quick die changes, just-in-time production (kanban), and empowering workers to stop the line to fix defects immediately.
Process Simulation and Analysis
In Lean Six Sigma, process simulation and analysis are crucial for identifying value-added and non-value-added activities. Techniques like drawing process maps and conducting detailed time and motion studies help organizations understand and optimize their workflows, reducing inefficiencies and improving overall process performance.
What is Lean Six Sigma?
Lean Six Sigma is a data-driven methodology aimed at improving process quality by identifying and eliminating defects and minimizing variability in process outputs. It uses statistical tools and follows a structured approach based on the DMAIC (Define, Measure, Analyze, Improve, Control) cycle to enhance process performance.
Lean Six Sigma Example
A practical example of Lean Six Sigma is the reduction of defect rates in manufacturing. By using statistical process control and rigorous data analysis, a company can identify the root causes of defects and implement targeted improvements. For instance, improving the precision of machine settings can lead to significant reductions in variability and defects.
How to Implement Lean Six Sigma
Implementing Lean Six Sigma involves several steps:
- Define the problem and project goals.
- Measure the current process performance.
- Analyze data to identify root causes of defects.
- Improve the process by implementing solutions.
- Control the improved process to ensure lasting gains.
The ‘Lean Six Sigma Transformation’
A successful Lean Six Sigma transformation requires strong leadership, a committed team, and robust infrastructure. Leadership must demonstrate support, provide resources, and reward achievements. The team should be skilled in Lean tools, Six Sigma methods, and project management. Continuous learning and adjustments to financial and planning systems are essential for sustained success.
Presentation of Results from an Actual Lean Six Sigma Implementation
In a real-world example, a manufacturing company implemented Lean Six Sigma to reduce defects and improve efficiency. By applying the DMAIC cycle, the company identified key areas for improvement, reduced defect rates by 50%, and increased overall productivity by 30%.
Lean Six Sigma Exercise (through process videos)
Participants will engage in video-based exercises simulating production processes. These exercises will illustrate the identification of value-added and non-value-added activities and the application of Lean Six Sigma principles to improve process efficiency.
A Case Study (if time available)
A detailed case study will be presented, showcasing the application of Lean Six Sigma in a specific industry. The case study will highlight the challenges faced, solutions implemented, and the positive outcomes achieved through the Lean Six Sigma methodology.
Lean Six Sigma Yellow Belt Certification Exam Registration for Participants
Participants will have the opportunity to register for the Lean Six Sigma Yellow Belt certification exam. The certification will validate their understanding of Lean Six Sigma principles and their ability to apply these concepts in real-world scenarios.
Post Workshop Activity Guideline
Participants are encouraged to continue their Lean Six Sigma journey by completing a post-workshop activity. They will draw a process stream map, identify value-added and non-value-added activities, and suggest at least one improvement. This activity will reinforce the concepts learned during the workshop and promote continuous improvement in their workplaces.
Instructor
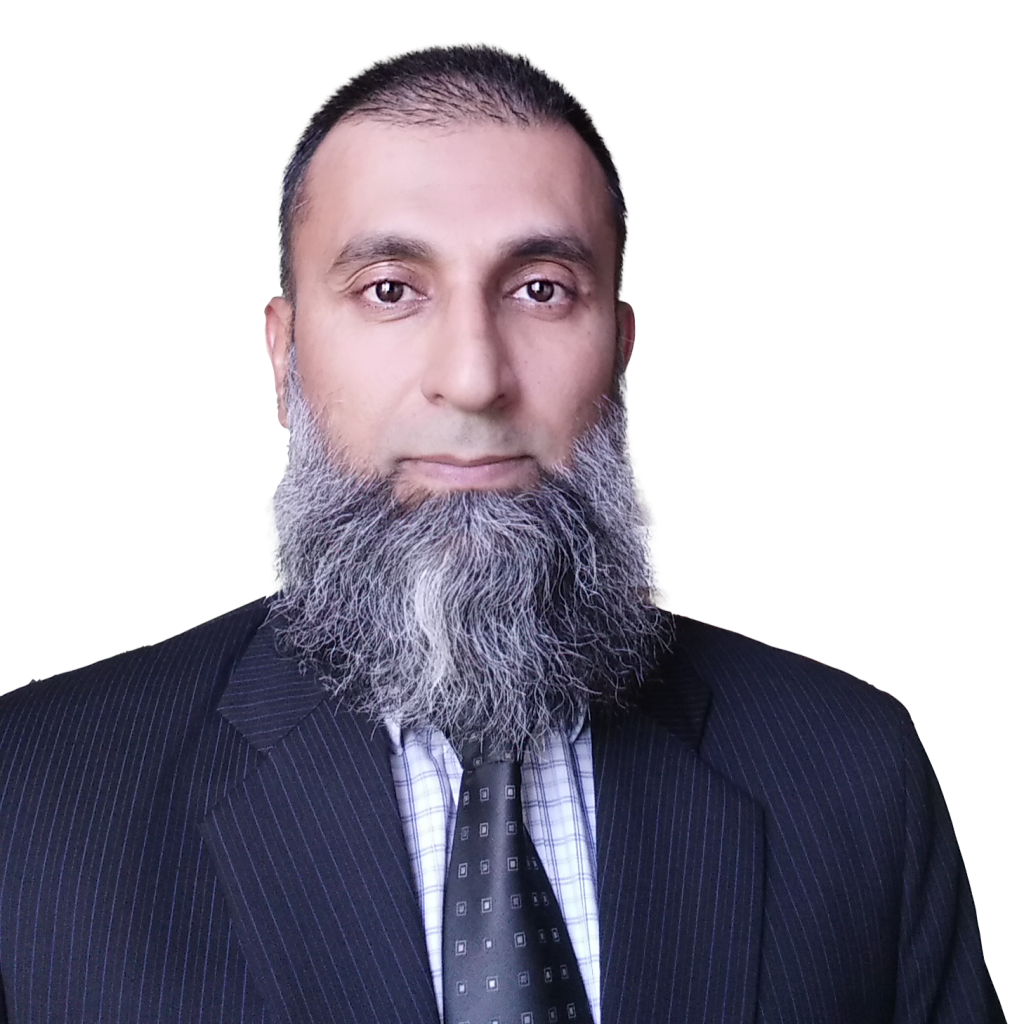
Syed Rehan Ali is the Founder of EDDS Consulting and Talents Park. He is a Master Engineer and an Entrepreneur with over 22 years of experience in operations and project management in industries like Automotive, Ordnance, FMCG Packaging, Furniture, Construction, Development Economics, Marketing and few others. Has accredited skills in Lean Six Sigma, project management, and business intelligence, allowing him to turn organizations and individuals into high-performance entities. He has trained over 1500 professionals (junior to C-level) and provided over 9000 hours of consulting to businesses in Enterprise Lean Six Sigma Transformation and Business Intelligence systems design and deployment.
He speaks regularly at various forums: Chambers of Commerce and Industry and Universities. He provides free training to charities and social welfare organizations, especially in education and health care, where possible.
LinkedIn Profile
thanks for info
You are welcome